Author: Texman
Union Budget 2024-25 benefits MSME based textile industry – SIMA
Coimbatore 23rd July 2024
SIMA chairman has welcomed the announcement of reducing the BCD on Methylene diphenyl diisocyanate (MDI) used for the manuf [...]
Book Release: Sustainable Innovations in the Textile Industry
A new book titled: "Sustainable Innovations in the Textile Industry," edited by Roshan Paul, Thomas Gries of the Institut für Textiltechnik of RWTH Aa [...]
Automation of GST Refund for Textile Industry
The Textile Association (India), Mumbai Unit
(Registered under Bombay Public Trust Act 1950)
602, Santosh Apartment, 6th Floor, Plot No. 72-A, Dr. M [...]
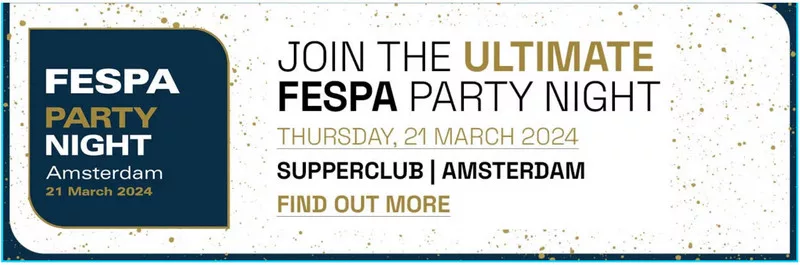
The 2024 FESPA Party Night on Thursday 21 March 2024
The FESPA Party Night is the ultimate event for the industry to network, unwind and enjoy an evening of live entertainment, music, drinks and grea [...]
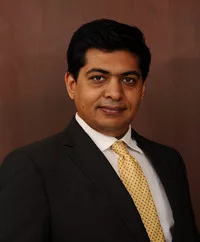
Avoid panic buying of cotton, says SIMA
Spiraling of cotton prices – avoid panic buying – SIMA
Coimbatore: The predominantly cotton based Indian textiles & clothing industry has been [...]
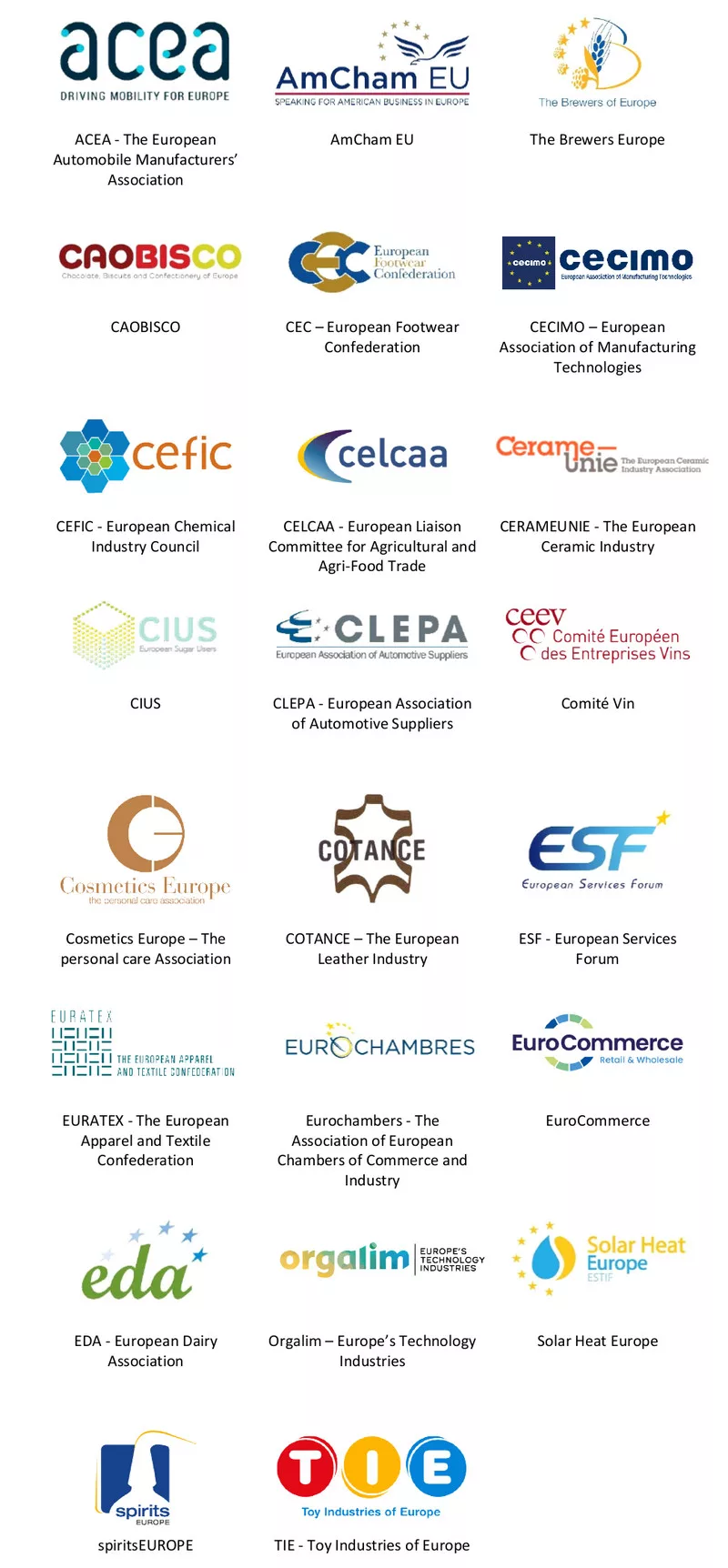
Industry Associations Joint Letter On The EU-Mercosur Agreement
Industry Associations' Joint Letter seeking rapid conclusion of the EU-Mercosur Agreement
Brussels – EURATEX and 22 industry associations sent a joi [...]
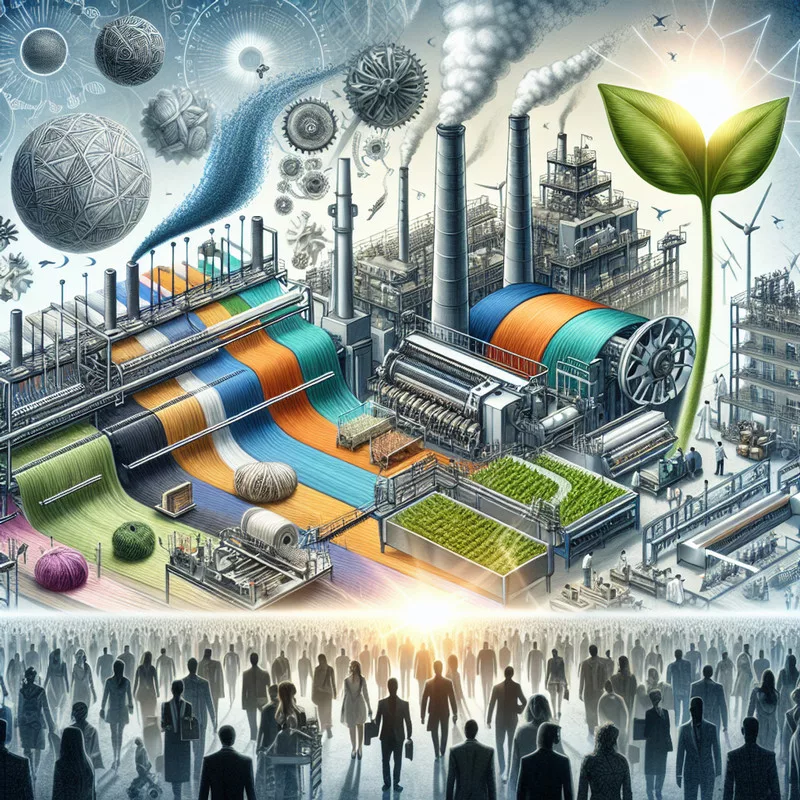
European Technical Textile Industry faces Tough Times
A diverse group of workers operating high-tech machinery in a textile factory, with raw materials being transformed into finished products, symboliz [...]
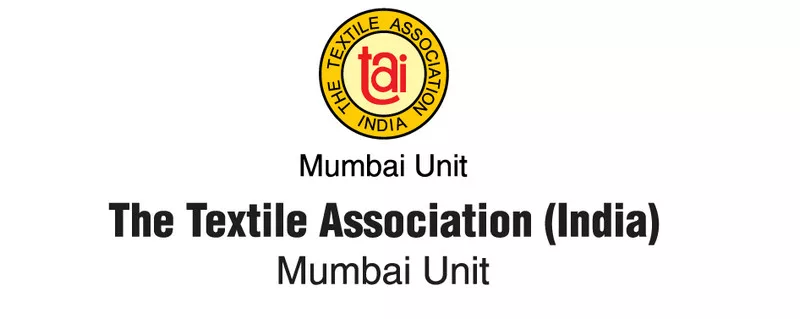
International Conference on Sustainability and Circularity
International Conference On Sustainability & Circularity: The New Challenges For The Textile Value Chain
Wednesday, 31st January 2024
Hotel The [...]

EURATEX Manifesto for Making the Industry Competitive
2024 is a Turning Point for the European Textiles and Clothing Industry
From 6 to 9 June 2024, European citizens will vote for a new European P [...]

Prolonged recession in the global textile value chain
Weakening demand, inflation, and geopolitics – major causes for prolonged recession in the global textile value chain – ITMF Chief
The textile [...]